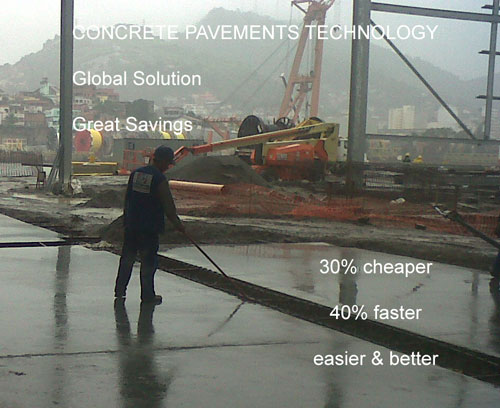
The line of behavior results from a complex interaction of the various components of the system, due to the demands imposed by railway composition in various environmental conditions. In order to fulfill the required demands, it is essential that each element performs its function, so that the system is stable, resilient and avoids either permanent deformations or wear of the components. The railway line solutions are characterized as follows:
The ballasted line is the oldest and is still today, structural solution. Its composition appears to have evolved very little over two hundred years, however, from the last forty years has been discussed the efficiency of its use for several reasons.
Alternative solutions to the ballasted line have emerged with the aim to reduce the problems in this type of structure. The non-ballasted track has been implemented in various countries such as Germany and Japan. Currently, this solution contained a large variety of structural designs,
Figure 1. : Schematic cross section of ballasted track
Another solution is mixed support line that usually used is a layer of bituminous mix in place of granular material in the sub-ballast layer. The mixed support line solutions have been developed in several countries, and best solution and widespread and successful application in Italy, with the high-speed lines.
In non-ballasted track, the ballast layer in the ballasted track is usually replaced by a layer of reinforced concrete slab or a layer of bituminous mixture (Figure 2.). The first group of solution which consists of rails, supported by sleepers laid or embedded in a concrete slab, being typically called line slab. For the second group, these solutions consist of sleepers made of reinforced concrete, supported directly on a bituminous layer, which replaces the ballast.
Figure 2: Different solutions via non-ballasted
There are currently two types of concrete sleepers in particular the bi block sleepers (reinforced concrete) and monoblock sleepers (prestressed concrete) (Figure 2.3).
Figure 3: concrete sleepers
The line slab solution, presents a wide range of structural designs. This variety results from different disposal possibilities and integration of the elements face the constraints imposed on the line. For example, in figure 4. are presented six different types of line design
Figure 4. : Several concepts via flagstone
When compared to the solution ballasted line, the line not ballasted is defined with three new layers
1 - Top layer in concrete slab (CSL - concrete supportive layer) or bituminous mixture (ASL - asphalt supportive layer) - this layer receives the reinforcement of the slab and distributes the loads transmitted by the carriages to the lower layers, respecting demanding durability requirements.
If reinforced concrete slabs are used it should assure a controlled cracking standard and ensure frost resistance and defreezing resistance.
In the case of bitumen support layers, conditions similar to the motorways/highways construction must be considered, however obeying more stringent criteria.
2 - Aggregates layer treated with hydraulic binder (HBL - Hydraulically Bonded Layer-
- This layer lies between the CLS (or SLA) and lower granular layer, degrading the loads to the lower layers. It is composed of inert materials and specific glanulometry, treated with a hydraulic binder.
The line In tunnels, bridges or more economic solutions is usual to eliminate this layer, provided that the thickness of the upper concrete slab is increased or improvement measures of the layers located immediately below are carried out;
3 - Layer of granular material, with properties similar to the sub-ballast (FPL - Frost protection layer): supports the layer treated with hydraulic binder and distributes the loads into the foundation layers. It must have a certain resistance to freezing and defreezing when and where it is relevant, as well as provide an acceptable drainage to the line.
The use of non-ballasted line as a solution for new railway lines enables a reduction in maintenance costs and increased stability of the line, allowing greater safety regarding the movement of carriages with increasingly higher speeds.
Regarding the foundation platform, it is necessary that this present deformations reduced to minimize the differential settlements throughout the project life.
Nowadays several solutions with high quality levels for lines not ballasted are available, thanks to the work developed in recent decades. Most of these solutions present life project for approximately 60 years, almost without requiring maintenance works.
Given the problems caused by granular sub-ballast, in some high-speed lines it arose the need to seek solutions for these matters. For such purposes soils were improved with cement to achieve acceptable CBR values. In addition to these solutions, in the first existing high-speed lines, bituminous mixtures were applied as sub-ballast in some countries.
Figure 5. shows the typical structure adopted by some countries.
Figure 5. : Typical section of high-speed lines
THE SOLUTION
The SPWS CONCRETE SLAB-FOUNDATION SYSTEM
The base being formed by EPS blocks (High density polystyrene at 30/kg / m3 at least) placed directly over the natural compacted ground.
Over it a plastic film of 0.2 mm, which function is only to allow the concrete to retract freely without anchoring and preventing it to crack while concrete retracts,
High strength resilient concrete is immediately laid down supported by our unique steel load transfer plates.
Our unique steel load transfer plates, which are anchored alternately on one side and the other of the concrete slabs, do allow transmission of the stresses caused by loads to all the adjacent slabs and accept differential settlements of the ground up to 25mm, but always ensuring the perfect continuity of the pavement..
The joint inductors, manufactured in plastic or galvanized steel, are placed over the steel load transfer plates to ensure the precise location of the joint opening, that simultaneously prevent the infiltration of all liquids to and from the base, forwarding them to the floor drain.
The end of the rails should never coincide with the joints.
THE PRICE OF THE BASE IN EPS, SHOULD BE AROUND €5.00/M2