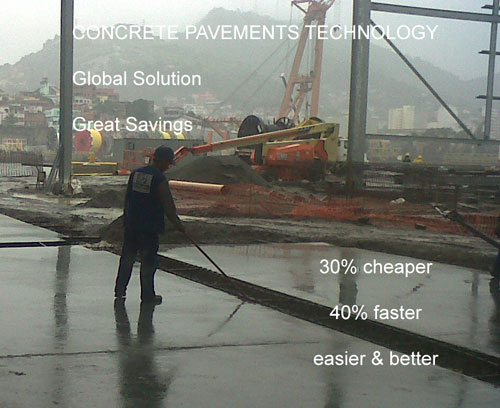
PHASES OF CONSTRUCTION
WAREHOUSE-BRAZIL works were carried out in 2012. It gives an idea of the construction speed allowed by our technology.
Here you shall see that the team of workers is 8 men, that the transfer plates are placed in the longitudinal and transverse positions so they transmit the loads to all slabs around it (here you see the first lane (row) being constructed), and while the concrete is being spread on the ground (light equipment is used) it follows immediately its flatting and its finishing.
By the end of the day the concrete is sawed in fresh and final finishing follows.
At last the anti sun is spread over the slabs to avoid evaporation, once the sun is now focusing the slabs.
The first lane (row) of the pavement is completed at the end of the first day. Using only light equipments we can achieve to construct with our technology until 1.200 square meters a day.
OTHER DATA OF THIS PAVEMENT
Natural soil in Brazil is clay but at the site it had a CBR of 7%
No based was used, except under the steel cutting machine concrete was spread over natural ground.
Slabs of 6m x 6m with a thickness of 15 cm
Pavement calculated for 5 tons punctual loads
EXECUTION AND GLASS OF WATER TEST
FACTORY BRAZIL AND GLASS WATER VIDEO TEST– is from a metalworking factory in which EPS was used only on the base of the steel cutting machines.
The glass water test proves that no vibration is transmitted to the contiguous slabs, what is quite important in all industries that use precision machinery.
Other data for this pavement:
Natural soil in Brazil is clay but at the site it had a CBR of 8%
No base was used except under the steel cutting machines. There EPS was used as a base.
Concrete was spread over natural ground, except under the steel cutting machine.
200 tons dynamic knock
Slabs of 5m x 5m with a thickness of 16 cm
Pavement calculated for 13 tons axel loads (loaded trucks with steel must enter the facility)
TECHNICAL EXPLANATION
ELUCIDATION OF THE TECNOLOGY USING A MODEL